PODCAST (in French) – Industry 4.0: competitiveness benefiting workers (not the other way around!)
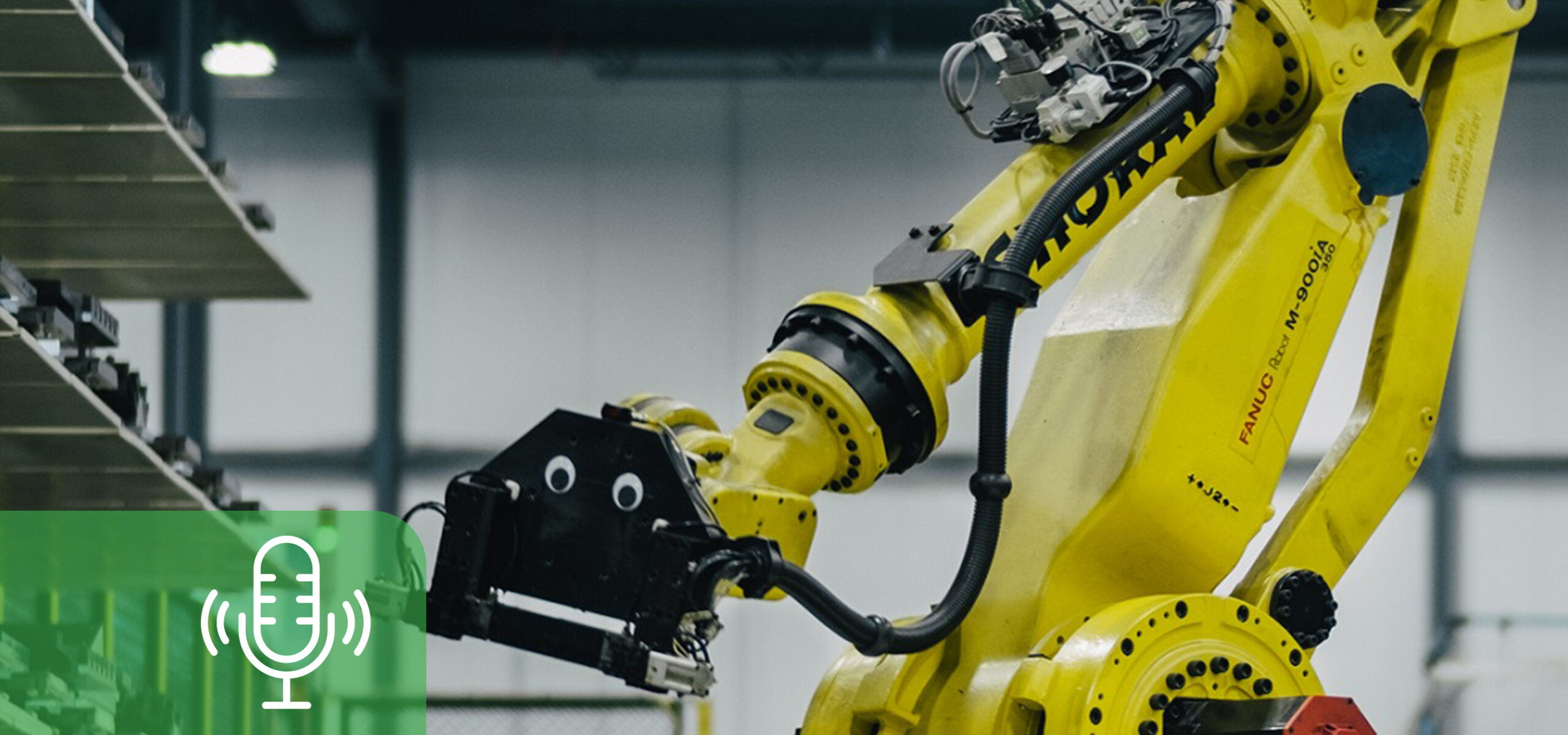
After mechanization (1.0), mass production (2.0) and digital automation (3.0), the manufacturing industry is entering its fourth great wave, one where artificial intelligence and communication help machines make productivity gains while increasing the value of workers’ roles. Two Fonds experts weigh in.
If you compare how robotization (3.0) combined with globalization resulted in a lot of job losses in North America at the turn of the century, Industry 4.0 has a very different kind of human impact since it counterbalances the lack of candidates during the North American labour shortage.
To listen to the podcast in French, click on the button below:
“Manufacturing industries had already made productivity gains by using robots, but with Industry 4.0, we layer on intelligence and communication; the entire business, not just the shop floor, is hardwired with the kind of sensors that allow automated machinery and software to coordinate their efforts automatically” says Nicolas du Parc, Investment Manager, Venture Capital and Technology for the Fonds.
“This intelligence translates into greater productivity, reduced consumption of resources, and greater safety. Basically, 4.0 isn’t in the business of replacing humans, but helping them in their work.”
Increasing quality of life and safety
He gives the example of Omnirobotic., a Laval firm and Fonds partner, that has integrated artificial intelligence in the robots currently in use in paint and powder coat processes.
“For instance, in a plant that makes a large variety of parts to be painted, it’s a human that currently does it, since it’s impossible to reprogram a robot for each part. The worker doing the painting is exposed to volatile chemicals in the process, and then inspects the piece to make sure it is painted correctly. With Omnirobotic’s technology, the robot will reprogram itself automatically depending on the geometry of the part, paint the part, and then the employee can carry out the inspection more safely without exposure to paint vapours,” du Parc explains.
Because it’s in solidarity with workers, whose savings it invests in local companies, the Fonds is sensitive to this human side of things, he adds.
“Our view on 4.0 is it’s a chance for workers to develop their capabilities to better contribute to the company’s productivity while flourishing in their work, with better quality of life and improved safety. In every one of our 4.0 related investments, we make sure that jobs will be maintained and that change will be positive for both people and the environment.”
A question of competitiveness
However, clarifies his colleague Martin Latreille, Investment Manager, Industries, the push for 4.0 is above all driven by a crying need for competitiveness by local businesses.
“Companies have already lost ground against the Americans over the past 15 years. Furthermore, the pandemic has shown they would benefit from simplifying their supply chains so they are less dependent on external factors. So they not only have to optimize their production, but all their business activities: inventory, procurement, customer service, etc.,” Latreille says.
He offers the example of Fonds partner Maibec., which gained a lot by automating the packaging of the cedar shingles it sells throughout North America, and continues making improvements to its painting processes as well. According to Latreille, the Lévis company is the perfect example of the extent to which technological transformation will become the definitive factor in how competitive Quebec manufacturers will become going forward.
Quebec expertise shines
The good news for Quebec companies who want to take the plunge is that they will find plenty of automation expertise locally. To name just a few such providers, there’s Excelpro, a leader in automation and industrial electrical services with 275 employees and Worximity, a Fonds partner company that optimizes the collection of production data for creating real time dashboards that help speed up decision making and reduce waste.
Also, to promote networking between companies seeking to automate and those that can help, the Fonds has gotten involved in the Regroupement des entreprises en automatisation industrielle (REAI.), an automation industry association. Its 135 members have a combined revenue of over $1.3 billion. That’s the kind of initiative that has helped Quebec industry attain a 45% automation level, versus 39% in Ontario.
“It’s important to bring these players together, because keep in mind that these 4.0 technologies don’t come ready out of the box, they are for the most part custom made. Then they have to be integrated into existing processes, not just at the technical level but on a human level, so you don’t only need sufficient technical support but also an enlightened approach to change management,” Latreille says.
Nicolas du Parc cites the recent automation plans adopted by Meloche Group., which looked great on paper but whose implementation depended on buy-in from staff. The Fonds connected the company with Asthuce Group, its team of multi-sector experts, that proposed forming discussion groups to help identify worker needs, understand their fears and come up with solutions going forward. This helped demonstrate the project’s benefits to staff while letting them input their own improvements, something that’s helped them adhere more easily.
Strawberry towers and other visions of the future
“The role of the Fonds as a venture capital investor is to help local expertise flourish, and help manufacturers avoid having to go to Europe or Asia in search of solutions. We want to help prepare champions that are not only going to respond to local needs here at home, but also compete on global markets,” du Parc says.
In Quebec, the typical 4.0 candidate is a manufacturer that produces a lot of different parts but in smaller volumes, also known as High Mix, Low Volume producers. Almost three quarters fall into this category according to du Parc, in fields ranging from aerospace to manufactured homes to the jewelry industry.
“Beyond each company’s individual efforts, our entire economy is being pulled to transform. We can imagine how, one day, instead of trucking in strawberries form California, we would grow them in the parking lot of the fruit store, without pesticides, in completely automated towers all year long with a very light carbon footprint. Bold players of this kind can come here and shake up our companies, but our own are just as capable of giving our companies a boost by strengthening their 4.0 efforts,” du Parc says.
As far as change management is concerned, it must include involvement and communication according to Latreille.
“The main 4.0 challenge is a human one, because it can have an unforeseen impact on the company culture. There are adjustments to be made, while supporting staff. Automating repetitive tasks is part of it, but which will have the greatest return? By studying the question together the members of an organization will find their most advantageous path going forward.”
Continue reading on this subject
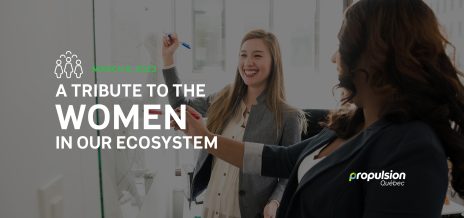
A TRIBUTE TO THE WOMEN IN OUR ECOSYSTEM – A portrait of the situation in the public domain
For a long time, the transportation sector consisted mostly of men. In the past ten years or so, more and more women can be found around discussion tables, in management roles and on executive boards of different leading corporations and organizations in our ecosystem.
Read more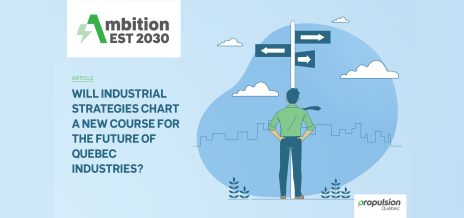
Will industrial strategies chart a new course for the future of Quebec industries?
The Quebec economy—and more broadly the world economy—faces multiple challenges: the climate crisis, supply chain problems, labour shortages, inflation, etc. Quebec has an abundant supply of resources, know-how, and expertise; however, the next points on its agenda should include structuring, developing, and planning industrial activities.
Read more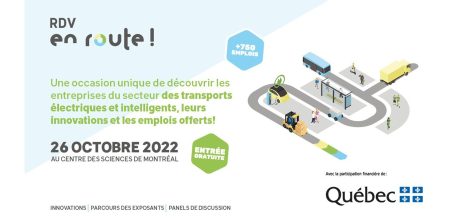
The electric and smart transportation industry is taking action to address the labor shortage through the En route! project!
Propulsion Québec, the cluster for electric and smart transportation (EST), is undertaking the En route! to Careers in EST project aimed at showcasing Québec’s know-how and attracting new talent to promote access to a qualified workforce.
Read more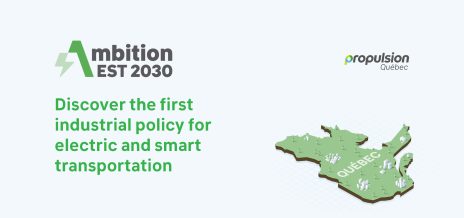
Ambition EST 2030 : a roadmap for propelling Quebec to the forefront of the electric and smart transportation industry by 2030
Propulsion Québec, the cluster for electric and smart transportation, is announcing Ambition EST 2030, a roadmap for the electric and smart transportation (EST) industry developed in partnership with Deloitte.
Read more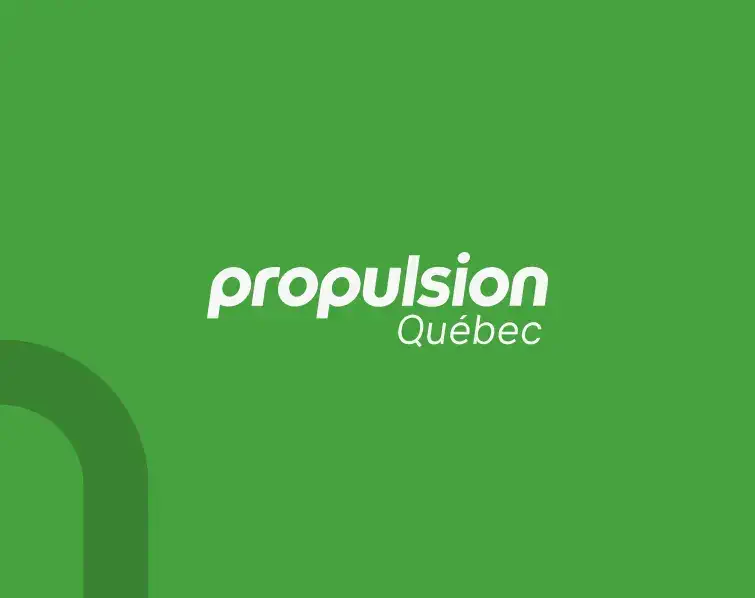
Quebec’s Growing EV Industry Drives New Jobs But also the Need for Reskilling
Quebec has emerged as a significant player in the Canadian electric vehicle (EV) industry, with expanding ability to compete internationally. New jobs and skills will be needed along with workforce development solutions, training, reskilling, and upskilling.
Read more